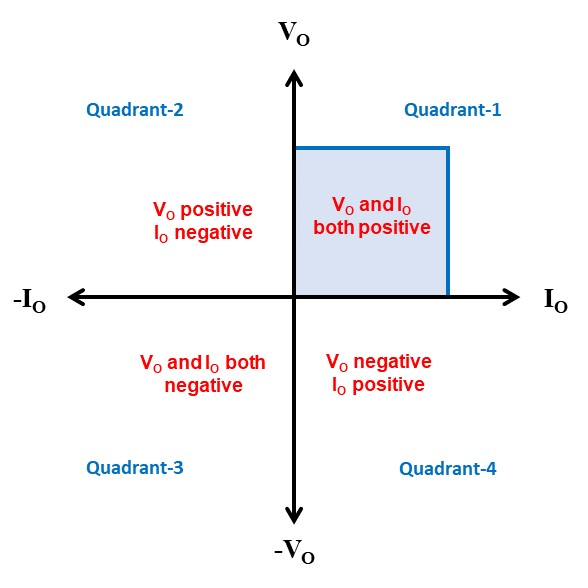
- The step-down chopper provides positive voltage and positive current at all times. So this is a first quadrant chopper
- This chopper is also known as Type-A chopper
- The power flow in type-A chopper is always from source to load (power is positive)
By turning the switch ON and OFF periodically, the voltage source can be connected and disconnected periodically from the load. By this action,chopped load voltage (Vo) as shown, is obtained from a constant DC supply of magnitude (Vs)
Note: The output voltage remains same for any type of load but the load current waveform will be different for different types of loads as explained below
The DC-DC converters can operate in two distinct modes with respect to the inductor current
For a step-down chopper, the value of the inductance that determines the boundary between CCM and DCM is given by
Lb = (1 - D) R / 2f
Step-down Chopper | Step-up Chopper |
---|---|
Vo = D * Vs | Vo = Vs / (1 - D) |
![]() |
![]() |
When the switch is on, load is directly connected to source. Vo = Vs |
When the switch is on, a short circuit path is created. The output voltage is zero and the inductor charges via the short circuit path. Vo = 0 V |
When the switch is off, load is disconnected from the source. Vo = 0 V |
When the switch is on, the voltage source and charged inductor will supply power to the load together. Vo = Vs + Vind |
Output voltage (Vo) is always lesser than the input DC voltage for all 0 ≤ D ≤ 1 | Output voltage (Vo) is always greater than the input DC voltage for all 0 ≤ D ≤ 1 |